When you’re managing a heavy equipment fleet, your primary goals are productivity, safety, and efficiency. Closely managing your fleet’s utilization is one of the most important ways to keep your heavy equipment operation running smoothly. Tracking and managing targeted fleet utilization metrics can give you the information you need to monitor and manage equipment usage, maintenance and repairs, crew productivity, and asset value.
Focused fleet utilization metrics provide critical information needed to monitor and manage equipment usage, maintenance and repairs, worker productivity, and asset values.
In this guide, we give you everything you need to start managing — and eventually maximizing — your fleet utilization. We will define fleet utilization, explain how to calculate equipment utilization, and advise on the best metrics to track when you want to keep your fleet operating at maximum capacity.
Inside this guide:
- What is fleet utilization?
- Why is fleet utilization important?
- How to calculate fleet utilization
- Six fleet utilization metrics you should be tracking
- How to maximize fleet utilization
- Five fleet utilization tips for heavy equipment contractors
What Is Fleet Utilization?
Fleet utilization refers to the amount of time your equipment fleet is in operation on a given workday. Analyzing your fleet utilization can help you identify operational bottlenecks and areas of improvement.
Typically, you express a fleet utilization rate in percentages, but the calculations can be complex. Understanding the ins and outs of fleet utilization calculations can help you manage your heavy equipment fleet by tracking critical metrics, analyzing utilization data, and pinpointing areas of improvement.
Why Is Fleet Utilization Important?
Maximizing your utilization helps increase your profitability by making your operation more efficient and productive. The equipment fleet is a critical part of your heavy machinery operation.
Paying attention to your fleet utilization allows you to protect some of your business’s most crucial assets. But fleet utilization is about more than just understanding how often your equipment is in use. Critical fleet utilization data also lets you track production and establish safe, sustainable operations.
Before deciding the best way to track utilization metrics in your organization, let's cover the benefits of tracking your fleet’s utilization, so you can decide which metrics matter most to you. The benefits of tracking utilization include the following:
Increased Fleet Productivity
Fleet utilization analysis can help you determine where your work schedules, labor distribution, and workflow can be addressed to improve efficiency. Rather than purchasing new haul trucks, for example, you might use utilization numbers to determine route changes or adjust your staffing.
Tracking utilization metrics like equipment usage can also help you make better, more informed decisions when buying new equipment. For example, if a 47-meter pump is only being utilized 25% of the time, and you have a 32-meter pump that is being utilized 100% of the time, you may consider adding another 32 meter pump to your fleet, or otherwise you may want to consider trying to seek out more jobs that will require a bigger pump.
Better Operational Efficiency
Fleet utilization can help you control operating costs and establish a fair market rate for your goods and services. By tracking usage, you can determine the relative asset value of your equipment.
Tracking operational efficiency also helps you reduce wear and tear on equipment. You can make the most of your heavy equipment usage without overloading, underloading, or causing undue strain.
Alignment With Consumer Demand
Reviewing fleet utilization helps you use your equipment efficiently by letting you analyze and meet changing consumer demand. In addition, it allows you to determine whether you need more or less equipment to meet consumer demand.
For instance, imagine you’re having a hard time booking new jobs because you rarely have trucks available to take on the work. Understanding your fleet utilization rate can help you figure out whether this is a scheduling issue, or whether you need to invest in more trucks for your fleet.
Improved Worker Safety
When addressing fleet utilization, most heavy equipment managers focus on the vehicles. But you may not realize that carefully managing fleet utilization is also important for keeping your crew safe. For example, you can reduce the potential for dangerous equipment failures by tracking your most frequently used equipment for maintenance and repair needs more than the gear you use less often. Without tracking equipment usage, adjustments like this are impossible. You can reduce the potential for dangerous equipment failures by tracking equipment usage.
With greater worker safety, you can also mitigate the number of workers’ compensation claims and on-the-job injuries, reducing downtime and helping boost productivity. A safer work environment also improves employee morale and reduces turnover.
By incorporating safety procedures into your fleet management and utilization plan, you can retain productive, trained employees. This can also translate to less money spent on recruitment, training, and onboarding.
Compliance With Regulatory Requirements
The Occupational Safety and Health Administration (OSHA) establishes stringent requirements for construction and other heavy equipment operations. Tracking metrics for fleet usage helps you manage maintenance, repair, load capacity, and staffing to comply with regulatory requirements.
Not only does this help you ensure worker health and safety, but it also reduces costs. You pay less for equipment repairs and downtime. In addition, regulatory compliance helps you avoid costly fines and penalties.
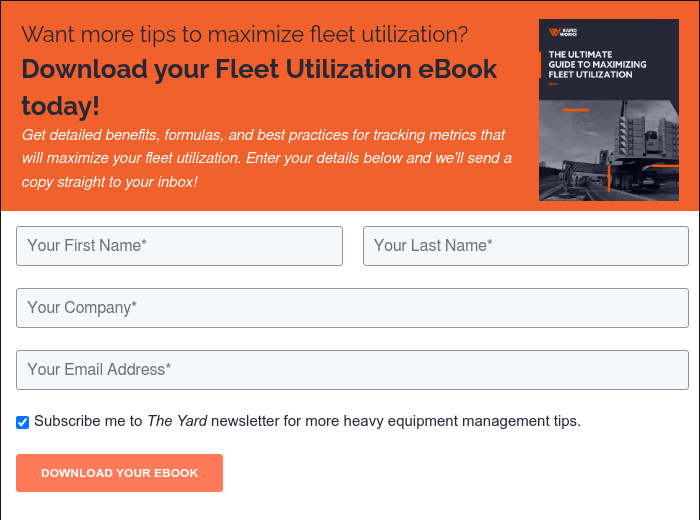
How To Calculate Fleet Utilization
Fleet utilization calculations vary depending on the market and equipment usage. For example, heavy equipment fleet utilization for an electric utility will likely differ from utilization in a mining operation or commercial construction project.
In this section, we’ll show you how to calculate your fleet’s utilization rate so you can keep track of performance over time. We’ll discuss key metrics and show you how to use that information to calculate utilization accurately.
A standard fleet utilization calculation typically includes the following:
- The number of vehicles in your fleet
- The maximum possible operating hours or mileage
- The number of actual operating hours worked or miles driven
With these three numbers, you can calculate the your fleet utilization with the following formula: Fleet utilization (%) = (Working hours used / Total working hours available) x 100
Say for example you have a fleet of 10 vehicles. Each vehicle has a maximum capacity of 10 hours per day. Your utilization metrics show that your vehicles only operate for 8 of those 10 hours. Your utilization rate would be calculated as follows:
Fleet utilization (%) = (8 x 10) / (10 x 10)) x 100 = 80%
Once you understand your fleet's overall utilization ratio, you can use this information to pinpoint opportunities for improvement. Once you've got the basics down, there are a few things to consider when adjusting your fleet utilization formula for your business:
Billed Hours
At its most basic, your fleet utilization formula will focus on billed hours. You need consistent billed hours to ensure accurate fleet usage calculations. For instance, many companies calculate their equipment utilization based on 8–10-hour workdays and 5-day workweeks. However, if your company often operates on extended hours, your fleet utilization formula should account for this.
Weekends and Emergencies
Weekends and emergencies can significantly affect your unique utilization formula. Consider that some companies only work weekends and evenings or in emergency situations. For example, an electrical contractor may work extended hours after a big storm.
While all usage data is critical for utilization calculations, consistency is key. Keep your maximum possible number of available hours constant each month, and exclude outliers.
If your fleet is deployed for extended hours after a hurricane, for instance, your numbers for actual hours worked may skew your utilization calculation. Eliminating outliers in your work hours or mileage calculations can help you ensure accurate, actionable utilization data.
Seasonal Fluctuations
Your fleet utilization calculations should also account for seasonal fluctuations in usage. Heavy equipment utilization often decreases in the winter when frost, snow, and other inclement weather prevent construction and utility work. Consider adjusting your utilization calculations to account for these seasonal shifts.
A month-over-month fleet utilization analysis is an excellent way to more accurately account for fleet utilization in seasonal industries. For instance, your company can determine your total usage hours and then calculate the month-over-month average for the full year.
You can also review your company's utilization rate on a monthly basis and track fluctuations. This allows you to accurately calculate your fleet's monthly utilization for your geographical area and pinpoint areas of improvement more consistently.
Six Fleet Utilization Metrics You Should Be Tracking
Every company has different operational requirements, which is why tracking your company’s metrics is crucial. Close monitoring and analysis of your fleet utilization numbers let you pinpoint areas of improvement and boost your company’s productivity.
If you aren’t already doing so, you should be tracking the following fleet utilization metrics.
1. Billed Hours
Billed hours are critical for creating a precise fleet utilization calculation. Tracking your workers’ hours lets you determine where scheduling and equipment utilization numbers diverge. You can learn how downtime, understaffing, and other worker challenges compromise your operation's productivity.
Data analysis of worker hours and productivity allows you to take direct action when your metrics do not align with your operating goals. The intersection between worker hours and productivity can reveal opportunities for training, hiring, and labor reallocation.
For example, perhaps your crane operator has significant idle time. You might consider cross-training them on other equipment or altering the crane operator's schedule to better align with the project’s needs.
2. Location Data
Tracking truck location can help you maximize fleet utilization. Tracking where and when your equipment operates and reviewing your truck usage helps you identify process inefficiencies and bottlenecks. Telematics solutions like Geotab and Samsara can help you get real-time truck location information.
Understanding your equipment movements also lets you keep an eye on labor usage. You can use this information to tighten up your schedule and reallocate resources to where they can be more effective.
RapidWorks’ ERP solution can help you double-check that your crew is on the clock only when your trucks are where you expect them to be. With tools like ours, your utilization no longer has to take a hit because of that Dunkin Donuts around the corner.
Ultimately, tracking your equipment helps you optimize operations and use your heavy equipment fleet most efficiently during work hours.
3. Operator Safety Practices
Data on worker safety practices helps you prevent injury and reduce liability, thus making your business more profitable. Incorporate safety procedures like pre-trip inspections and safety processes, and encourage operators to incorporate them into their daily operation schedule.
When you prioritize safety procedures, you also reduce downtime, equipment damage, and repair costs. Operators are more likely to catch issues during routine daily inspections, so they can be escalated for maintenance before becoming problematic.
4. Regular Machine Maintenance
Maximize your fleet utilization by scheduling and tracking periodic equipment maintenance. Routine maintenance is crucial for running a smooth heavy-equipment operation. Include regular equipment maintenance in your fleet utilization calculations to avoid costly downtime.
Regular equipment maintenance reduces the potential for broken components, damaged equipment, and employee injuries. Track your maintenance schedule and incorporate it into your daily operations to reduce inefficiency and enhance your overall profitability.
5. Equipment Repairs
Repairing equipment is an expensive but unavoidable aspect of managing a heavy equipment fleet. Minimize downtime and overhead costs by tracking your equipment repairs. You can use this data to analyze trends and catch issues before they occur.
In addition, you can project the time and resources typically necessary to complete equipment repairs. This helps you more accurately track your fleet utilization and plan for unavoidable downtime.
6. Fuel Usage and Mileage
Fuel usage and wear on heavy equipment can add up quickly and affect your operating efficiency. Tracking your fuel usage and mileage metrics can help ensure your equipment operates at maximum efficiency.
You can also use fuel usage data to discover equipment damage before it becomes dangerous. Higher fuel usage without greater mileage can indicate mechanical issues before they are readily apparent.
Finally, tracking mileage can help you keep your equipment on track for routine maintenance. Since regular usage can fluctuate, a maintenance schedule is not always reliable. Mileage tracking lets you keep your equipment well-maintained. This promotes a longer service life and reduces the potential for costly repairs.
How to Maximize Fleet Utilization
Maximizing your fleet utilization keeps your operation running smoothly while maximizing your profitability. High fleet utilization promotes overall operational efficiency, which can save you millions of dollars in overhead. Keep your fleet utilization high by following these steps:
Tailor Your Metric Analysis to Your Business
Every business has unique needs. Different operating requirements, standards, and equipment require an individual fleet utilization data analysis approach. Additionally, each project may have unique requirements.
Consider specific factors that affect your utilization. For example, say your concrete pumps experience excessive waiting time between pouring foundations in a large construction project. But they work long hours into the evening when pouring to ensure consistent drying time. Your utilization calculations and metric analysis might lead you to consider raising your hourly rates for the pump, since you might not be generating enough revenue from concrete yardage pumped.
On the other hand, if your fleet spends a weekend repairing a washed-out culvert after a flood, you may consider those hours as outliers when establishing your fleet utilization calculations.
Regularly Review Data for Continuous Improvement
Your fleet utilization metrics can change rapidly in response to a variety of conditions, including:
- Inclement weather
- Emergency situations
- Project delays
- Supply chain interruptions
- Demand fluctuations
- Market shifts
- Seasonal changes
- Priority demands and rush jobs
Monitor your metrics to ensure you can accurately analyze the data. Some utilization shifts, such as an emergency repair, may act as outliers. Others may signal an overall business shift, such as a busier winter season or increasing weather emergencies. Recognizing utilization shifts early can help you make necessary adjustments before they negatively affect your bottom line.
Establish Clear Processes and Procedures
Maximize your fleet utilization by establishing checklists and operating processes. When your workers know what to expect, they can conduct operations consistently. This consistency is crucial when tracking your equipment utilization.
Keep operations consistent and easy to monitor by creating uniform operating procedures. While many operations require a level of flexibility, less variation can help you ensure accurate usage numbers.
Consistent operating procedures allow you to interpret your utilization numbers more reliably and take appropriate action. For instance, consistent utilization above a certain threshold may mean you need to obtain additional equipment. Similarly, usage below an established threshold may require repurposing or selling equipment.
Provide Comprehensive Training
Ensure your fleet operates with maximum efficiency by promoting clear, consistent training for your equipment operators. A major source of inefficiency in heavy equipment operations is lack of training.
Workers with insufficient training may take longer to complete tasks, which in turn compromises your fleet utilization. Poorly trained employees are also more likely to make mistakes, which can lead to damaged equipment, employee injuries, and unnecessary downtime.
A trained, confident employee will be more productive and know where they fit within the project scope. They will also make sound decisions without the need for constant oversight and direction.
Emphasize the Project Scope
Improve your fleet utilization numbers by emphasizing the full scope of the project, which gives your workers a common goal. Workers who see how they function within the operation are more adaptable and confident, helping to foster employee confidence, productivity, and efficiency.
Employees who understand the project scope may be more likely to pitch in and help co-workers on unassigned tasks. Shared responsibility and employee empowerment improve morale and increase productivity. A strong team with a focus on project scope can help you better meet your project budgets and deadlines while maximizing your fleet utilization.
Prioritize Safety Procedures
Employee safety is crucial for optimal fleet operation. By making safety procedures a priority, you maximize your equipment utilization in the following ways:
- Avoiding unnecessary cost and liability
- Ensuring regulatory compliance
- Preventing equipment damage
- Reducing equipment repair costs
Incorporating standard safety procedures helps you avoid costly medical expenses, as well as potential fines for regulatory violations. With consistent documented safety procedures, you can also more accurately calculate and maximize your actual equipment utilization.
Ideally, safety processes become automatic and an inherent part of the overall process. Workers accustomed to safety routines can complete checks, inspections, and other procedures rapidly. This increases employee productivity in addition to protecting worker health and safety.
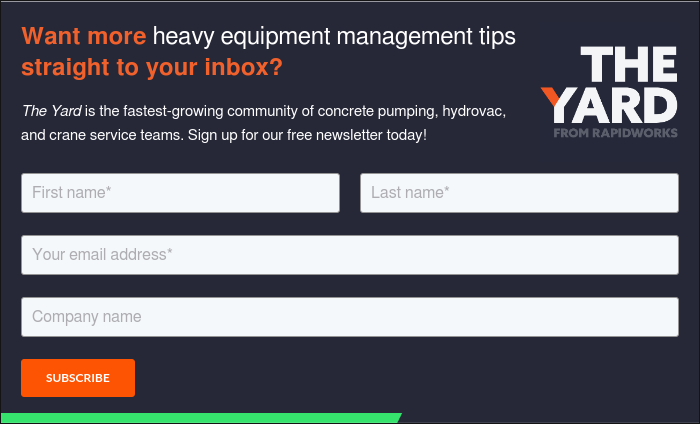
Five Fleet Utilization Tips for Heavy Equipment Contractors
Heavy equipment contractors must contend with the added wear and safety concerns common in more rugged and extreme environments. Fleet utilization tracking and analysis become especially critical when you must operate and maintain millions of dollars worth of machinery.
Heavy equipment applications may include:
- Construction
- Demolition
- Utilities
- Transportation
- Mining
- Oil and gas operations
- Marine and offshore
- Agriculture
- Forestry
- Landscaping
- Waste management operations
- Military and defense
Managing a sizable fleet requires you to focus on efficiency in every aspect of your operation. Operations often require specialized equipment used in unique ways. For instance, a construction company and a utility company may both require cranes, but the use cases will differ. Consider the following factors when creating a utilization plan ideal for your heavy equipment operation.
1. Reduce Equipment Idle Time
Idle time is sometimes unavoidable for certain industries and projects. However, tracking idle time lets you see where to focus so you can increase fleet productivity as much as possible.
Fleet utilization reports can help you track when your heavy equipment is sitting idle throughout the workday. Review your project schedule and labor distribution to maximize equipment usage.
2. Maximize Equipment Capacity
Establish operating schedules and procedures, and ensure optimal efficiency by tracking your equipment's capacity through targeted metrics. Whether you are lifting, loading, carrying, or unloading, understanding your equipment capacity is critical for efficient utilization. Fleet utilization data can help keep your equipment usage within the ideal load range for optimal equipment efficiency.
Maximizing loads without overloading helps keep operations moving smoothly and efficiently. At the same time, you should aim to use your equipment to its full capacity. Underloading can extend your project timeline, lower worker productivity, and reduce fuel efficiency.
3. Reduce Fuel Consumption
Anything that makes it harder for your equipment to operate smoothly can increase fuel consumption, so it’s important to keep up with preventative maintenance, such as:
- Clogged filters
- Worn or dirty fuel injectors
- Worn or dirty hoses
- Dirty or poorly lubricated joints, axles, gears, and other mechanical equipment
- Frayed or broken belts and connectors
Regular cleaning, maintenance, and inspections can prevent expensive fuel wastage. Consistently analyzing your fuel consumption data can help pinpoint such issues before they require expensive repairs and downtime.
4. Minimize Equipment Wear
Monitor equipment wear by tracking equipment utilization and maintenance. Reduce your asset depreciation by conducting regular maintenance, cleaning, and repairs on your equipment.
Track your load capacity and equipment usage requirements to ensure you have sufficient equipment, time, and staffing to avoid unnecessary wear. Having insight into load distribution, capacity, and maintenance operations can help reduce wear and extend your equipment’s service life.
5. Invest in Fleet Management Software
Using fleet management software like RapidWorks makes it easy to calculate your heavy equipment fleet utilization and ensure optimal operational efficiency.
RapidWorks offers premier software solutions for heavy construction equipment companies throughout North America, Europe, and Australia. Our versatile fleet management tools allow you to monitor multi-faceted construction operations and streamline complex processes.
At RapidWorks, we understand that timing and efficiency are critical components of a successful construction project. We can tailor our software solutions to meet the particular needs of any heavy construction application.
Our customers use our Rapid ERP, Telematics GPS, and Rapid On-the-Go mobile apps to manage heavy construction projects, including hydrovac excavation, concrete pumping, and mobile crane dispatch.
Learn more about ways RapidWorks software solutions can help you maximize your fleet utilization. Contact us today to schedule a demo.
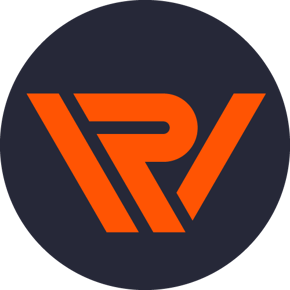