Your fleet has a thousand moving parts, from vehicle usage to labor and fuel costs. You're responsible for keeping everything running on time, in good condition, and for maximum profit. Tracking these fleet utilization metrics is key to understanding how to get more out of your trucks and equipment.
In this article, we’ll review seven key fleet utilization metrics:
- Fleet Capacity
- Vehicle Utilization Rate
- Crew Capacity
- Work Capacity
- Time to Repair (Downtime)
- Preventative Maintenance On-Time Completion Rate
- Fuel Consumption
These key performance indicators (KPIs) provide practical insights you can use to help boost revenue and capacity. Using KPIs to manage your fleet gives you the concrete data you need to make the best decisions for your business.
1. Fleet Capacity
Fleet capacity is a metric used to understand the maximum amount of work a fleet can take on in a given day, week, or month.
Here's how to calculate fleet capacity for a given week:
Fleet Capacity = (Total Trucks * Total Billable Hours Available) / Days of the Work Week
However, no single workweek looks the same in the heavy equipment industry and depends entirely on seasonality, available personnel, and workloads. You'll need to set this number according to your estimated work week and continuously review capacity numbers to understand how to adjust goalposts week by week.
Fleet management software like RapidWorks automatically calculates and tracks capacity for every truck, so you can always see how much work your fleet is capable of.
2. Vehicle Utilization Rate
After calculating fleet capacity, you'll want to calculate how close your fleet comes to working at maximum capacity. This metric is known as the fleet utilization rate.
Calculate vehicle use with the following fleet utilization formula:
Vehicle Utilization (%) = (Total Hours Billed / Total Billable Hours Available) x 100
The higher the utilization rate, the better your profits. To improve utilization, you can:
- Sell underutilized, out-of-use, or high-downtime vehicles
- Repurpose underutilized vehicles or operators for other projects
- Reduce non-billable hours by improving routes and maintenance schedules
Using fleet management software can help dispatchers calculate utilization faster and more accurately than manually tracking hours and utilization for every truck. For example, RapidWorks automatically keeps track of the amount of time every truck bills, and generates visual utilization reports that update in real-time.
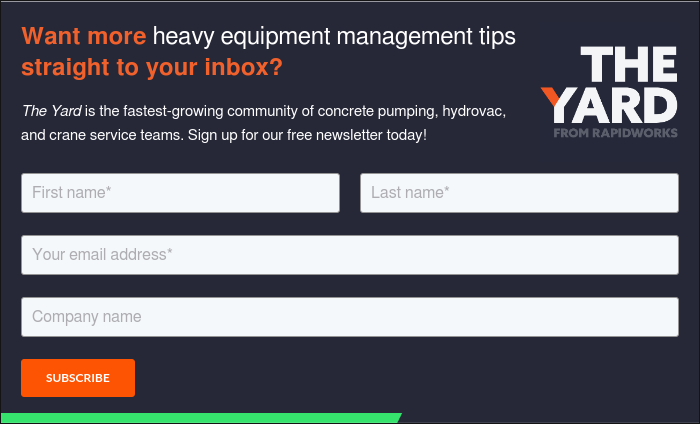
3. Crew Capacity
You need to track vehicle usage to bring down costs, but tracking labor is equally important.
To understand your crew's maximum capacity, use the following formula:
Crew Capacity = Total Number of Operators * Total Billable Hours Available
Calculating your max billable hours always depends on company policies. Getting to this number requires breaking down the different types of time spent throughout the day:
- Working (billable) hours
- Non-work (idle) hours
- Break hours
- Travel hours
After collecting this information, use the following formula:
Total Billable Hours Available = Total Hours Worked – Non-Billable Hours.
Once you've worked out your billable hours, run the crew capacity formula to track your labor.
4. Work Capacity
Fleet utilization metrics require breaking down numbers by individual vehicles and operators, known as work capacity. These numbers vary depending on vehicle type and operator schedules. To do this, issue time management sheets with relevant slots for each data point for each operator and vehicle.
Some top-line work capacity metrics for heavy machinery include:
- Idle Time Per Truck = Total Idle Time / # of Trucks
- Idle Time Per Operator = Total Idle Time / # of Operators
- Revenue Per Truck = Total Revenue / # of Trucks
- Revenue Per Operator = Total Revenue / # of Operators
- Revenue vs Cost (Profit) Per Truck = Total Revenue Per Truck - Total Cost Per Truck
- Revenue vs Cost (Profit) Per Operator = Total Revenue Per Operator - Total Cost Per Operator
In heavy machining, the amount of accomplished work depends on the type of truck and the nature of the job. For example, you'd measure work capacity by the total amount of concrete pumped. To track this metric, you'd take stock of the amount of raw materials pumped instead of the maximum amount that could be pumped if you filled the max amount of billable hours.
5. Time to Repair (Downtime)
Tracking fleet maintenance is critical to increasing your profits, as surprise repairs can lead to massive downtime.
To measure downtime, use this formula:
Downtime = End of Downtime - Beginning of Downtime, in hours.
By understanding downtime per truck, you can set up a rotation schedule for maintenance to maximize billable hours. Rotating maintenance increases efficiency and means you have a bit more wiggle room to accommodate surprise repair needs.
6. Preventative Maintenance On-Time Completion Rate
Maintenance is always an enormous cost of running a fleet. However, preventative maintenance can significantly reduce the likelihood of costly emergency repairs and reduce downtime in the long run.
One way to measure the effectiveness of your preventative maintenance program is to understand your compliance rate. You can calculate compliance with this formula:
Preventative Maintenance Compliance = (# of Vehicles with Completed Preventative Maintenance / Total # of Vehicles) * 100
Improving your on-time completion rate for regular maintenance will help increase compliance over time, which should reduce your total maintenance costs and downtime.
7. Fuel Consumption
Fuel accounts for 22% of the cost of vehicle ownership. The key metric to track fuel consumption is miles per gallon (MPG).
Miles Per Gallon = Miles Traveled / Gallons of Gas Consumed
Take a look at your average and then consider the following actions to reduce fuel consumption:
- Provide operators with routing tools to travel to job sites faster.
- Confirm all jobs the day before to reduce wasted trips from last-minute cancellations.
- Use map-based locations instead of addresses to provide accurate job locations and reduce wasted trips.
- Route trips straight to second jobs instead of returning to the office.
Fleet management software like RapidWorks puts heavy equipment crews in direct contact with dispatchers, helping reduce unnecessary travel time and keep mileage down while telematics providers like GeoTab and Samsara can help you automatically keep track of fuel consumption.
Unlock Profit Growth With the Best Software
Ready to use fleet management software to begin taking full command and control of your fleet? Schedule a demo and discover why RapidWorks is the leading solution for heavy equipment teams.
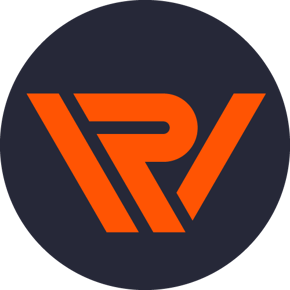