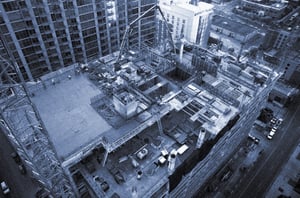
Top 10 Concrete Pump Hazards and Safety Precautions
Concrete pumping is a dangerous gig. Of course, there’s the initial danger that comes with working with heavy machinery, but pumping is also a highly technical process. Safely operating complicated equipment like booms and pumps demands more than just slapping on a hard hat and gloves.
To avoid danger, you need to be aware of the danger. Then you can apply the right concrete pump safety precautions to stay safe.
Below we'll run through ten concrete pump hazards along with some safety tips for avoiding them.
1. Hose Hazards
One of the most common concrete pump hazards comes from emptying the concrete delivery hose. When full of concrete, hoses can weigh more than 376 pounds. Upon releasing compressed air to clean the hose, pressure pockets can make the hose whip around chaotically, as shown in the video below, which can lead to severe injuries or equipment damage.
Avoiding hose hazards requires you to take certain safety precautions:
- Stand back whenever compressed air is being released, ensuring everyone is distant enough to avoid being struck by sudden whipping movements.
- Avoid using a double-end hose or double-S attachment. These attachments are much heavier and can cause greater damage if a hose whips out of control.
- Take air readings at the point of discharge to monitor pressure levels.
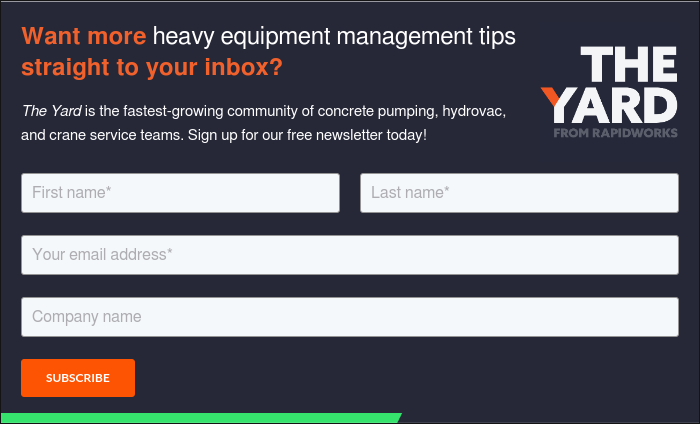
2. Power Lines
Power-line contact can be lethal, potentially leading to a loss of arms or legs or even death.
Usually, power-line hazards result from operator error. To avoid the devastating effects, contractors must follow these safety steps:
- Train employees on power-line safety and inspections.
- Maintain a minimum of 20 feet of clearance between the power line and the pump unit.
- Develop a system of verifying the power-line stamp for every job site.
- Request the power-line stamp up front, and inquire if there are power lines around the job site or in the setup, cleanup, or pour area.
3. Concrete Burns
When skin is exposed to wet cement, the alkalinity can cause burns. Left untreated, it can result in blood poisoning and scarring.
Typically, burns occur because operators don't dress for the occasion. Here are a few tips to prevent concrete burns:
- Consider your protective gear, head to toe, to ensure no skin is exposed.
- Scrub burn areas with a pH-neutral or slightly acidic solution, such as vinegar.
- Wash all concrete out of your clothing before wearing it again during work.
4. Electrical Issues With The Truck
Concrete pump trucks can experience electrical issues when they don't undergo routine maintenance, causing equipment to malfunction or shocking operators as they troubleshoot.
Proper system maintenance for electrical-related safety issues includes:
- Check the alternator to see if it needs to be replaced by testing the output voltage, ensuring that it's at least 13.6 VDC.
- Check the battery and ground connections, ensuring they're clear of obstruction; if they're dirty, clean them and tighten any loose terminals.
- Test the battery's amp loads to ensure it's operating at adequate strength.
5. Hydraulic Leaks
Leaks arise from damaged fittings, connections, and hoses. Failure to address these leaks can result in faulty or inoperable equipment. Oil also has a harsh effect on the environment.
Check your equipment to prevent avoidable leaks. Act fast when responding to hydraulic leaks and follow these steps:
- Shut off the equipment and pinpoint the source as soon as a leak is detected.
- Catch as much of the hydraulic fluid as possible and keep it from spreading.
6. Boom Awareness and Placement
Given their sheer weight, booms require your undivided attention. Reckless or unattentive boom operation can damage things like lights, HVAC systems, sprinklers, or the concrete pump itself. As such, booms require a thoughtful setup and placement strategy.
To ensure safe boom placement:
- Be aware of the boom's location at all times.
- If your boom comes into contact with any other object, thoroughly check for damage before returning to work.
- Never move a boom pump without first folding the boom and outriggers into the travel position and then locking them in place.
- Never attempt to use the boom for hoisting.
7. Rough Mixes
Rough mixes happen during the batching process. Essentially, a rough mix is a pour that's concocted with the wrong material or ratio. It’s unstable for pumping because it yields concrete that wears out fast or is structurally unsound.
Given that different jobs require various mix types, keep in mind a few key rules to perfect the batching process:
- Ensure the rock quantity is right to obtain the right plasticity for passing through the hose.
- Check the rock size to ensure the mix doesn't pack together when mixing.
- A proper mix often requires multiple sizes of rocks to obtain a good flow.
8. Oil Leaks
Oil leaks are hazardous because the liquid can reach up to 176 degrees Fahrenheit, which can cause severe burns. Similarly, oil-injection injuries occur when people try to stop high-pressure oil leaks with their bare hands, often resulting in gangrene.
- Never attempt to stop a high-pressure oil leak with your hand, even if it's gloved, or with a rag.
- Always shut down the machine and let it rest before identifying and addressing the leak.
9. Holding Valves
Removing a holding valve is extremely dangerous. Done incorrectly, it can cause burns, impact injuries, or both.
The main risk factor here is pressure, as pressurized valves can shoot out and seriously injure nearby workers or damage nearby equipment.
When removing holding valves, exercise the following precautions:
- Ensure there's no remaining pressure before removing the holding valve.
- Don't remove a holding valve that hasn't had time to rest or one that doesn't have support for the boom.
- Unlatch all holding valves slowly.
10. Compressed Air
Some say you should “never say never,” but you should never use compressed air for blockage removal.
Using compressed air to empty a full boom causes pressurization. When the pressure gets too high and someone opens a clamp with pressure still in the boom, the hose could explode, spewing concrete throughout the job site and potentially injuring those nearby.
On top of remembering to avoid using compressed air to empty a boom, follow these safety precautions:
- Because air pressure can remain in a boom from the day before, always check the pressure levels before removing the clamps.
- Remove the clamps using a tool like a shovel, which creates a safer physical distance between you and the boom.
Take Safety Seriously With RapidWorks
Any team looking to prioritize concrete pump safety needs to use the best tools to manage vehicle inspections and job-site safety audits. RapidWorks makes these vital tasks super easy, allowing owners to run safety checks right from their phones once on the job site.
Get more done, and safer. Centralize your safety process and check out RapidWorks today!
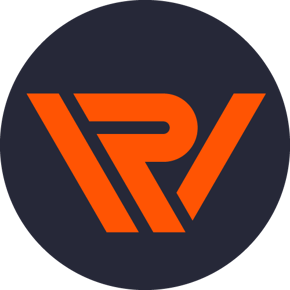